Exactly How Professional Product Packaging Equipment Fixing Solutions Minimize Downtime and Boost Productivity
Expert packaging device fixing solutions are crucial in minimizing downtime and improving productivity through specialized diagnostics and prompt treatments. The effects of such solutions prolong beyond immediate repair work-- unpacking the more comprehensive influence on functional effectiveness exposes important insights right into lasting performance techniques - packaging machine repair service.
Relevance of Timely Services
Timely fixings of product packaging makers are essential for keeping functional effectiveness in any type of manufacturing setting. When equipment malfunctions or breaks down, it can lead to significant disruptions in assembly line, leading to enhanced downtime and shed earnings. The longer a product packaging equipment remains out of order, the better the influence on total performance, potentially creating hold-ups in satisfying orders and lessening client complete satisfaction.
Along with the instant financial ramifications, postponed repair services can cause extra considerable damage to the equipment. Components that are not resolved immediately can degrade even more, requiring more costly fixings or full replacements, which can have been prevented via timely treatment. Normal maintenance and timely repair services can boost the lifespan of packaging makers, ensuring that they operate at optimal efficiency degrees.
Buying specialist packaging device repair service solutions is vital for mitigating these threats. A proactive technique to repair services not just maintains production schedules however additionally cultivates a society of integrity within the organization. By prioritizing timely repair work, services can preserve their one-upmanship, enhance resource allotment, and inevitably boost their bottom line through boosted functional effectiveness.
Competence in Diagnostics

Effective diagnostics not just facilitate quick identification of problems however also boost the general integrity of product packaging operations. By conducting extensive evaluations, professionals can evaluate the wellness of important elements, making sure that even small irregularities are dealt with promptly. This interest to information minimizes the threat of unforeseen malfunctions, which can lead to expensive downtime.
In addition, professional diagnostics give valuable insights into functional patterns, enabling businesses to make educated decisions concerning equipment upgrades or modifications. By leveraging these insights, business can maximize their product packaging procedures, bring about enhanced performance and performance. Ultimately, buying diagnostic knowledge is necessary for companies looking for to maintain seamless procedures and maintain high requirements of top quality in their packaging procedures.
Preventive Maintenance Advantages
Preventive upkeep complements professional diagnostics by proactively resolving prospective concerns prior to they materialize into severe troubles. By carrying out a structured preventive maintenance program, companies can dramatically reduce the risk of unanticipated machine failures, thereby minimizing costly downtime. Normal evaluations, cleansing, and components replacement help make sure that product packaging machinery operates at ideal efficiency.
Among the crucial advantages of preventive maintenance is its capability to extend the life expectancy of tools. By frequently maintaining equipment, services can prevent the intensifying effects of wear and tear that often lead to major repair work or substitutes. packaging machine repair service. This not only saves capital yet additionally enhances the total integrity of production processes
In addition, preventative maintenance adds to enhanced security problems within the office. By my latest blog post determining and correcting possible dangers before they escalate, organizations develop a much safer setting for their employees. This aggressive strategy not only shields employees but likewise fosters a society of obligation and vigilance.

Custom-made Service Solutions
Acknowledging the special needs of each company, personalized solution options for product packaging maker repair service offer tailored strategies that enhance operational performance. These services are developed to address specific challenges faced by various markets, making sure that maker downtime is minimized and performance is optimized.
Professional repair services sites start with a comprehensive analysis of a firm's packaging operations. By understanding the details machinery entailed and the needs of the production environment, service technicians can establish an individualized repair and maintenance plan. This might consist of specialized training for in-house personnel, the execution of anticipating maintenance innovations, or the stipulation of specialized support throughout peak manufacturing times.
Additionally, personalized remedies can integrate flexible service contracts that align with a firm's functional timetable, enabling for repair work to be executed throughout off-peak hours. By prioritizing the one-of-a-kind demands of each service, these bespoke remedies make certain that repairs are not only efficient yet also flawlessly integrate into existing workflows.
Eventually, the concentrate on personalization makes it possible for business to maximize their product packaging processes, causing boosted integrity and performance of equipment, which is crucial for maintaining competitive benefit in today's fast-paced market.
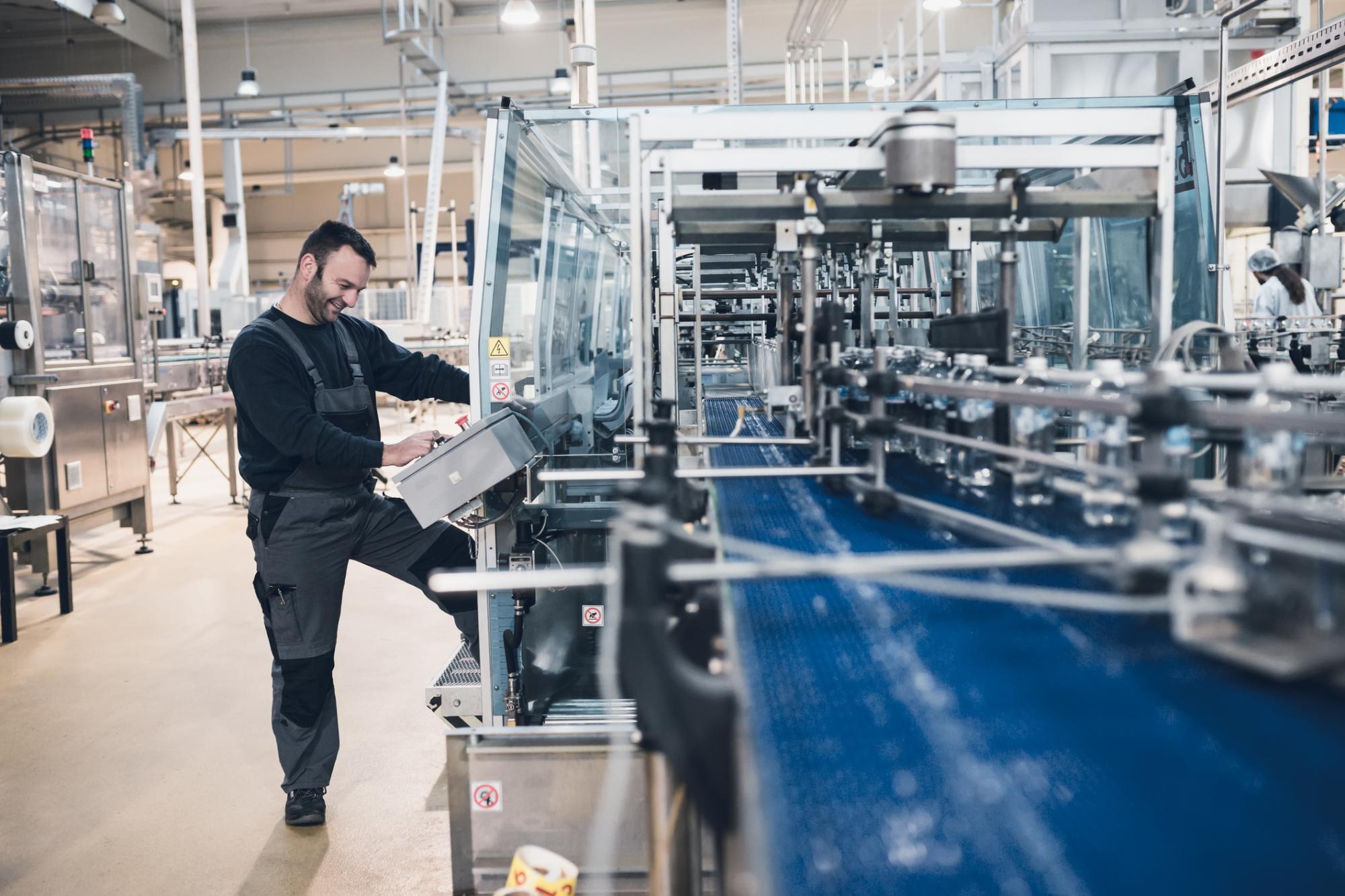
Effect on General Efficiency
Personalized service solutions not just address specific repair work needs but also play a considerable function in improving general functional effectiveness. By supplying targeted treatments, specialist packaging maker fixing solutions directly lower the regularity and duration of tools failings. This aggressive approach guarantees that assembly line continue to be functional, reducing disturbances that can bring about pricey downtime.
Moreover, reliable fixing solutions add to smoother workflows, as well-maintained machinery runs at optimal efficiency degrees. When equipments work properly, the quality of packaged products enhances, causing fewer problems and much less rework. This improvement not just enhances performance yet additionally enhances consumer complete satisfaction.
Additionally, routine maintenance and fast reaction times from repair work professionals foster a society of dependability within the organization. Employees can focus click here to find out more on their key jobs as opposed to fretting about possible devices malfunctions. Consequently, the total throughput of the production procedure boosts, enabling companies to fulfill need more properly.
Ultimately, the calculated investment in expert repair services equates to improved efficiency across all functional facets, making certain that companies can adjust and thrive in an open market. This synergy between upkeep and productivity is necessary for long-lasting success.
Conclusion
Finally, professional packaging maker repair work solutions play an essential function in decreasing downtime and enhancing productivity within manufacturing atmospheres. Prompt repair work, expert diagnostics, and precautionary upkeep add to the integrity of tools, while customized service remedies address particular functional requirements. The cumulative impact of these services results in boosted overall efficiency, making it possible for organizations to keep production schedules, maintain product quality, and efficiently satisfy market demands. Purchasing such services eventually drives sustained operational success.
Comments on “Enhance productivity with a quality packaging machine repair service.”